Metal forming is an essential manufacturing process that manipulates metal material into desired shapes by applying force. It produces specific geometries needed for various end-use parts and products. Understanding the most common metal-forming techniques is key for both manufacturers and buyers of formed metal components.
1. METAL ROLLING
Rolling is a metal-forming process that presses metal stock between two opposing rotating cylinders to reduce thickness and create uniformity. The opposing rotational forces shape the workpiece to achieve the desired cross-section.
HOW ROLLING WORKS
During rolling, the metal strip gets squeezed between the rolls as it passes through, flattening, thinning, or lengthening it. This reduces the thickness while smoothing and cleaning the surface. The distance between rolls determines the amount of compression and deformation applied to the starting metal piece.
APPLICATIONS OF ROLLING
Common rolling applications include:
➤ Producing sheet metal
➤ Manufacturing plates, strips, and foils
➤ Forming structural steel sections like I-beams and railroad tracks
➤ Creating cylindrical sections like pipes, rods, wires
2. METAL EXTRUSION
Extrusion pushes heated metal through a die opening to create long pieces with a specific uniform cross-section. The die forms the workpiece to the desired shape as it exits.
HOW EXTRUSION WORKS
During extrusion, a hydraulic ram forces the soft metal alloy into the die cavity under high pressure. As the metal squeezes through the shaped opening, it stretches and hardens into that form. The continuous extrusion process can create bars, tubes, and specialty profiles in long lengths.
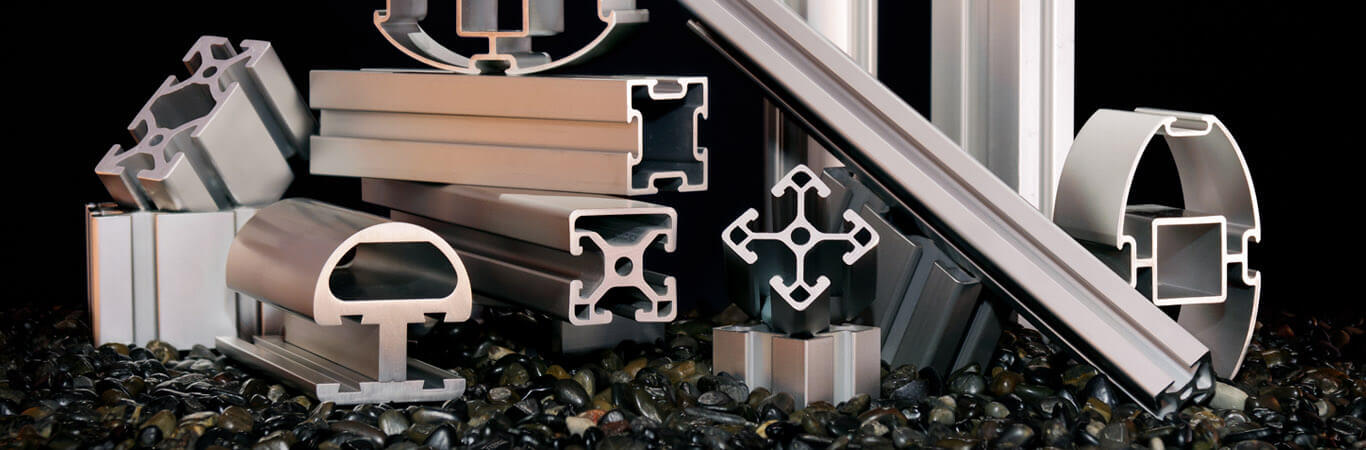
APPLICATIONS OF EXTRUSION
Typical extrusion applications:
➤ Aluminum window and door frames
➤ Pipes, tubes, and channels
➤ Rods and bar stocks
➤ Custom structural shapes
3. METAL FORGING
Forging uses localized compressive forces to mechanically form metal between design dies. Repeated impact deforms the raw material into high-strength finished parts.
HOW FORGING WORKS
In forging, the workpiece gets pressed between two dies that shift and shape the pliable metal when force is applied. The impressions from the dies form the desired geometry through a series of targeted high-pressure blows.
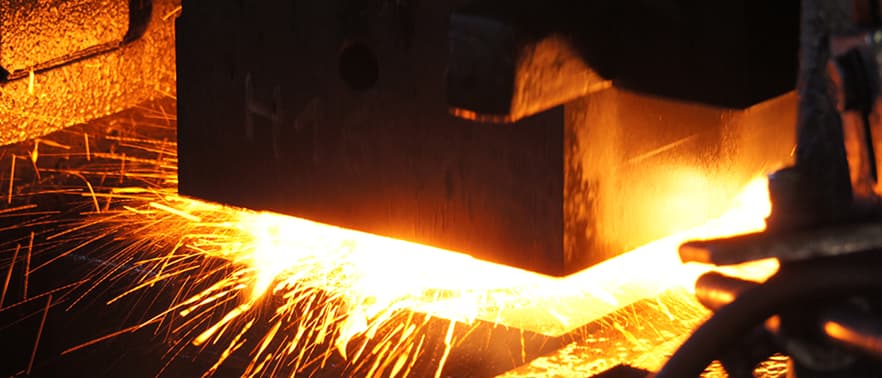
APPLICATIONS OF FORGING
Common forged parts include:
➤ Engine components
➤ Large bearings
➤ Cutting tools
➤ High-load transmission parts
4. METAL DRAWING
Drawing pulls sheet metal through a die to stretch it into various parts and assemblies with fine details. It produces lightweight components with dimensional accuracy.
HOW DRAWING WORKS
In drawing operations, the starting flat sheet gets gripped tightly and pulled through a shaping die cavity. This deepens the forms and compresses designated areas to make complex, drawn shell-like components.

APPLICATIONS OF DRAWING
Typical drawn parts include:
➤ Automotive bodies
➤ Aircraft fuselages
➤ Complex enclosures
➤ Culverts
➤ Medical equipment
➤ Tin cups
5. METAL STAMPING
Stamping presses sheet metal blanks between matched metalworking dies to mass-produce parts with custom geometries. It offers flexibility for both simple and complex components.
HOW STAMPING WORKS
The stamping press has a material-handling system to feed and locate sheet stock between the dies. It then presses the material to take shape through a series of cutting and forming steps during each stroke until achieving the final configuration.
