The purpose is to protect critical parts of components from exposure. Wires, parts, and components often need to be shielded from exposure to human contact, moisture, heat, dust, contaminants, or electrical currents. However, it can also be the case that the critical components must be stopped from coming into contact with the environment or with other parts of a machine.
The most common way to protect these critical elements is to house them in a sheet metal enclosure, providing a secure case view of the components. Sheet metal enclosures are used because metal is durable, malleable, and can be fabricated in several different shapes. Different types of metals have a wide spectrum of properties, so designers can fabricate sheet metal enclosures for an array of purposes.
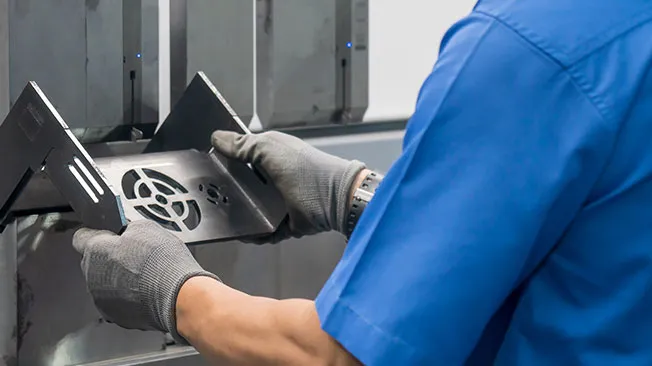
Why is it important ?
It’s difficult to overstate the importance of sheet metal enclosures for industrial designers. Any industry that designs products with sensitive parts or components or products that are to be used in extreme temperatures will require sheet metal enclosures for housing intricate details.
Sheet metal enclosures are used to shield sensitive components from other parts of a machine, from human contact, from temperature fluctuations, electricity, vibrations, or outside contaminants. Additionally, sheet metal enclosures are crucial for safeguarding critical parts in the event of a machine failure, ensuring their protection within specified dimensions of fabrication.
Examples of products that use sheet metal enclosures
Practically any item that is produced using metal fabrication will require a metal enclosure of some sort in stock. Precision sheet metal enclosures and small sheet metal housing can be found in everything from consumer goods to electronics to automobiles to aircraft. A desktop computer is housed in a metal enclosure and contains various parts that are housed in sheet metal enclosures.
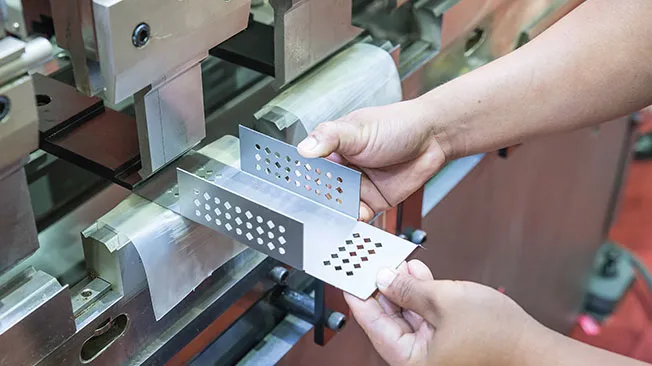
The wiring in audio mixing desks is protected from interference by sheet metal enclosures. Cars, boats, and aircraft use sheet metal enclosures to keep components separate and to protect vital electronic computer systems from fluids. A common household microwave or a refrigerator both require a sheet metal enclosure for housing their internal electronic components securely within boxes.
What materials are used for creating a piece?
Finding the right sheet metal solution depends on the nature of the machine or product being built. Once the requirements of the particular product have been determined, a designer must then decide on what metal to use. There are five main types of metal used for sheet metal enclosures.
Aluminum
Aluminum is incredibly lightweight, malleable, and is resistant to corrosion. There are various grades of aluminum but the two most commonly used for sheet metal enclosures are 5052 and 6061. An aluminum enclosure made of 5052 can be bent into a variety of shapes without cracking. While 6061 is more prone to cracking, it can be machined more easily than 5052 aluminum.
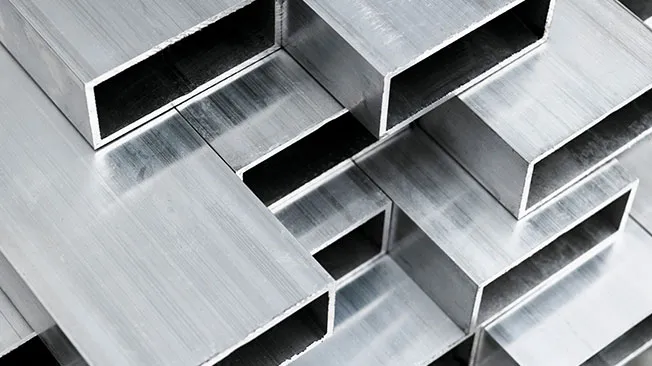
Stainless steel
Stainless steel is highly corrosion resistant as it contains nickel and chromium. It has a high tensile strength and so is usually used for sheet metal enclosures that must withstand high impacts or large amounts of vibration.
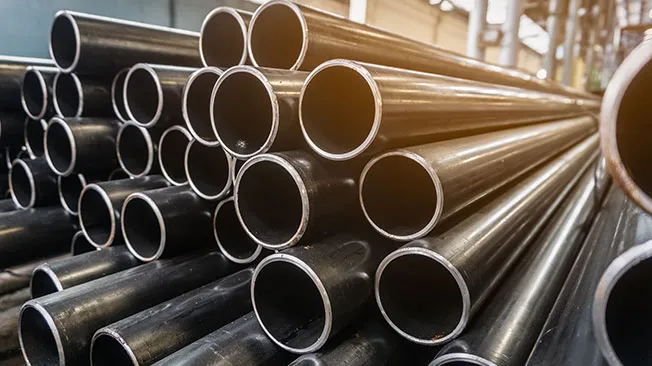
Galvanneal
Galvanneal is a steel material that has low rates of carbon and is commonly annealed and has a zinc coating to add strength. Galvanneal stands up well to moisture and is highly corrosion resistant so it is mostly used in products that will be exposed to fluids.
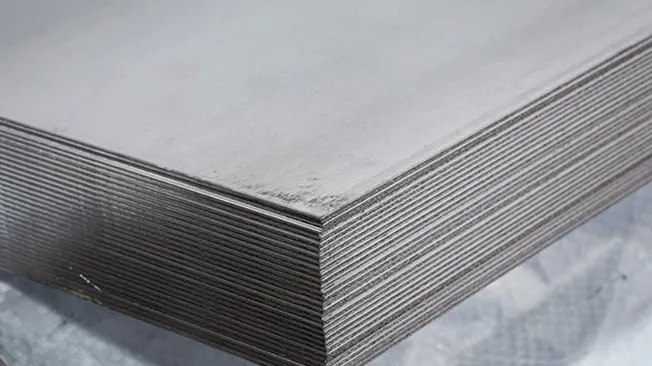
CRCA
CRCA is the acronym for cold rolled close annealed steel. Although it is prone to rusting if it is not coated, the stiffness and strength of CRCA make it ideal for sheet metal enclosures that are not going to be exposed to extreme conditions.
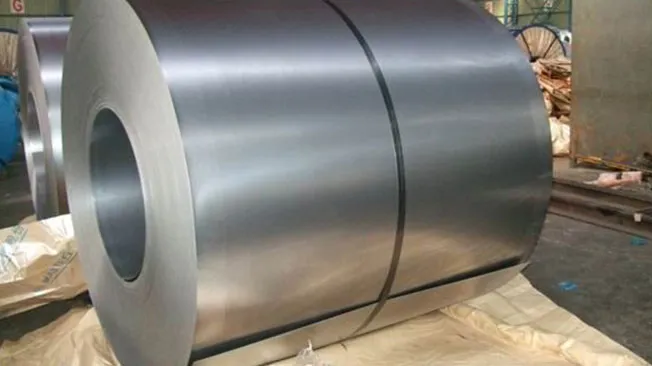
Copper
Copper is the least used of these metals when it comes to sheet metal enclosures, but it still has specific attributes that make it a good option in certain cases. Copper has high rates of thermal conductivity and electrical conductivity which means it is often used to build sheet metal enclosures for electrical products. The malleability of copper, however, means that many manufacturers choose other metals for their sheet metal enclosures.
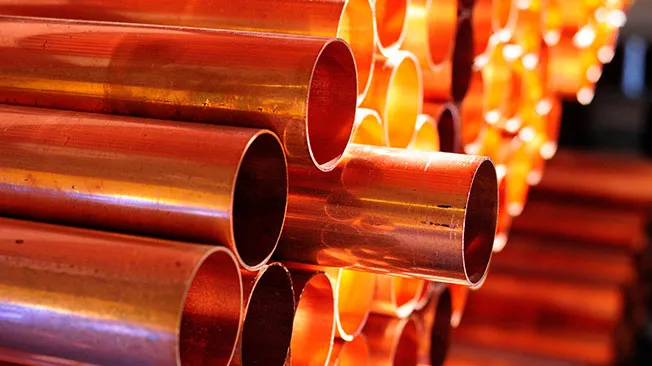
Common manufacturing processes for sheet metal enclosures
Various techniques are used to manufacture sheet metal enclosures. Sheet metal cutting is used to produce the sides and tops of a sheet metal box. Bending and forming sheet metal techniques are used to produce F-shaped, L-shaped, and U-shaped sheet metal enclosures. Stamping techniques such as deep drawn stamping and progressive die stamping are used to join sheet metal components together. Finishing processes for sheet metal enclosures include annealing, heat treatments, and hardening.
Applications of sheet metal enclosures
There are hundreds of ways in which sheet metal enclosures are used. The consumer electronics industry uses sheet metal for electrical enclosures that shield components from electricity. Industrial machinery and equipment often require sheet metal enclosures to keep components separate.
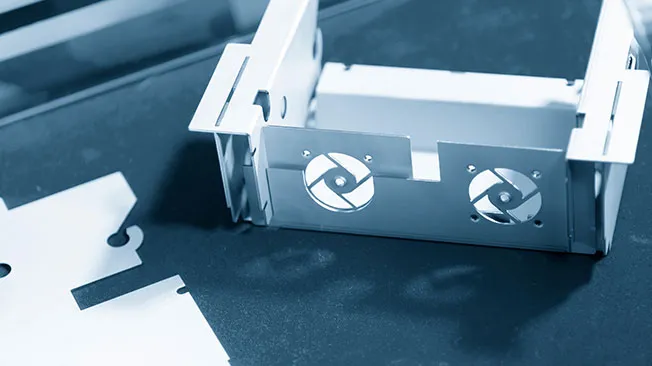
Most telecommunications and networking equipment are built with a sheet metal cabinet to keep the wiring safe. The automotive and transportation industries use sheet metal enclosures to protect computing systems, shield wiring, and stop fluid from corroding or contaminating sensitive components.
Advantages and limitations of sheet metal enclosures
Advantages of sheet metal enclosures
Sheet metal enclosures and sheet metal parts have numerous advantages over enclosures or parts made using glass, plastic, or other materials. Metal is incredibly durable and strong, so it has a longer lifespan and provides enhanced protection from environmental factors.
Sheet metal is also versatile and malleable, which makes sheet metal assembly and sheet metal manufacturing a relatively fast process when compared to other alternatives. Sheet metal is highly cost-effective and readily available from numerous suppliers.
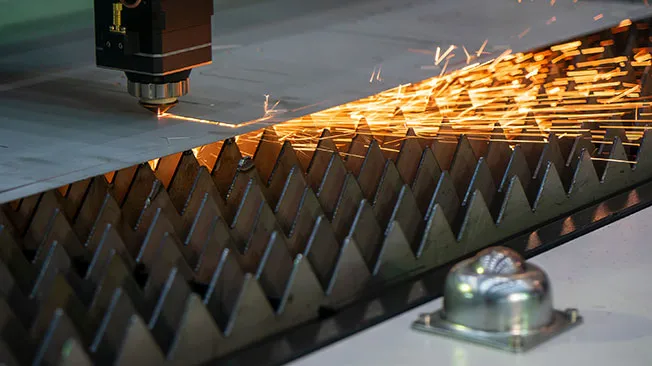