1. Introduction to Sheet Metal Fabrication
Sheet metal fabrication is a comprehensive manufacturing process that involves shaping, cutting, bending, and assembling metal sheets to create functional parts and structures. Its versatility has made it foundational in industries like automotive, aerospace, construction, electronics, and more. From car body panels to intricate electronic enclosures, sheet metal is essential for building robust, durable, and customizable solutions. Sheet metal fabrication has been practiced for centuries, evolving from hand tools to advanced machinery, and today it remains at the heart of industrial innovation.
2. Types of Sheet Metals and Their Properties
Understanding the different types of sheet metal is crucial for selecting the right material for any project. Steel, aluminum, copper, and brass each offer unique characteristics:
➤ Steel: Known for its strength and durability, steel is commonly used in construction and automotive applications.
➤ Aluminum: Lightweight and corrosion-resistant, aluminum is ideal for aerospace and transportation.
➤ Copper: With excellent electrical conductivity, copper is often used in electrical applications.
Each metal’s thickness, malleability, and resistance to wear make it suitable for specific applications, and choosing the right one ensures optimal performance.

3. The Sheet Metal Fabrication Process
The sheet metal fabrication process involves multiple stages:
➤ Cutting: Laser, plasma, and water jet cutting are commonly used to achieve precision cuts on metal sheets.
➤ Bending: Press brakes and folding machines shape the metal into specific forms.
➤ Forming: Techniques like stamping and deep drawing allow for complex shapes.
➤ Assembling: Welding, riveting, and other joining techniques complete the structure.
Each stage requires precision and expertise to maintain quality and consistency in the final product.
4. Advanced Techniques in Sheet Metal Fabrication
With the integration of CNC (Computer Numerical Control) systems, sheet metal fabrication has become more precise and efficient. Automated laser cutters and CNC-controlled press brakes are examples of how technology enables high-speed, high-quality production. Laser technology advancements also allow for more complex and intricate designs, which are now feasible in mass production.
5. Common Tools and Equipment Used
The industry relies on various machines, including press brakes, laser cutters, and punching machines, to handle different aspects of fabrication. Safety is paramount with these high-powered machines, requiring protective equipment and training. Recent innovations, such as automated bending machines, are also making production lines more efficient.
6. Applications of Sheet Metal Fabrication
Sheet metal fabrication’s applications are extensive:
➤ Construction: Roofing, ductwork, and structural elements
➤ Automotive: Body panels, chassis, and custom parts
➤ Aerospace: Lightweight, durable components for aircraft
➤ Electronics: Enclosures for computers, HVAC systems, and more
Its adaptability makes sheet metal essential across nearly every industry.
7. Design Considerations in Sheet Metal Fabrication
Designing for sheet metal fabrication requires understanding manufacturing constraints. Tolerances, material thickness, and allowances all play a role in a design’s feasibility. Proper planning in these areas helps reduce waste and ensures parts fit and function as intended.
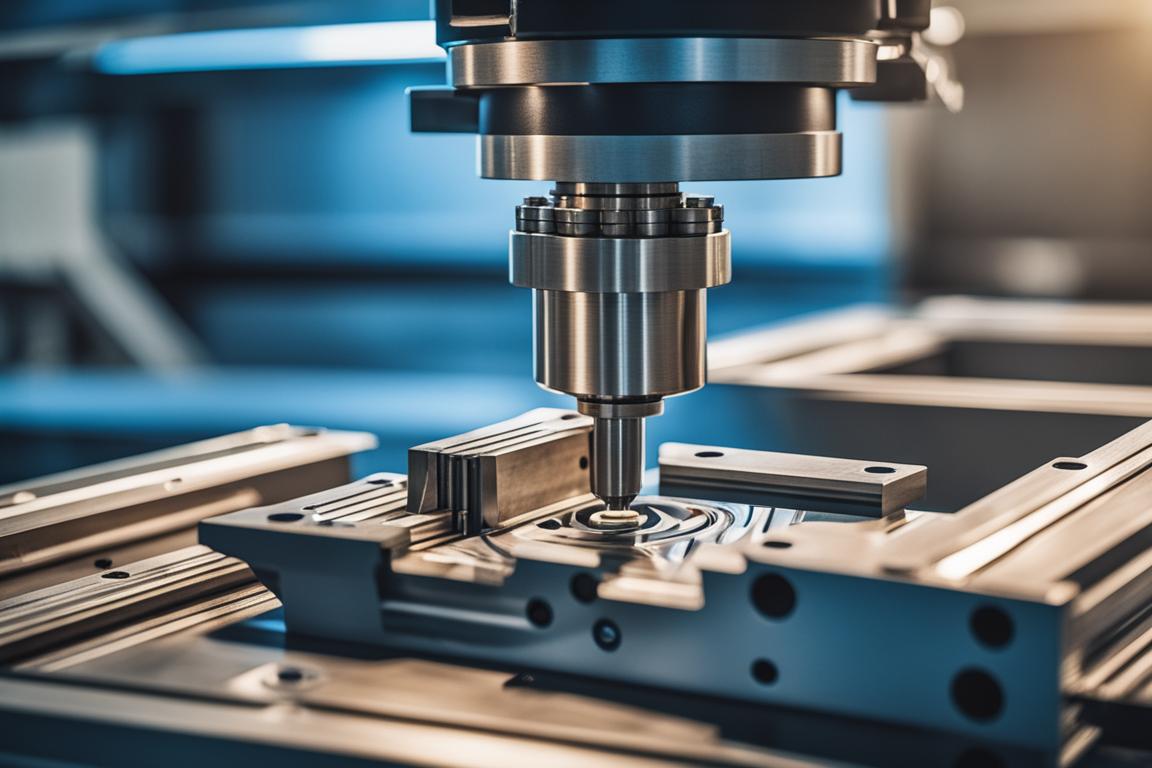
8. Sustainability in Sheet Metal Fabrication
Sustainable practices in fabrication are increasingly important. Recycling metal scraps, using energy-efficient equipment, and selecting eco-friendly coatings help reduce the industry’s environmental impact. Advances in recycling technology are also making it easier to repurpose materials, further contributing to sustainability.
9. Future Trends in Sheet Metal Fabrication
AI and machine learning are revolutionizing the industry, enabling predictive maintenance, quality control, and automated workflows. Robotics is also making an impact, particularly in welding and handling, as the industry moves towards greater automation. Additionally, innovations in recycling technology are helping make the industry more environmentally friendly.
10. Conclusion