Laser welding is a cutting-edge joining process that has revolutionized the manufacturing industry by providing a highly precise and efficient method for fusing materials together. This article explores the laser welding process, various techniques, and its wide-ranging applications across different industries.
The Laser Welding Process
Laser welding employs a high-intensity, focused laser beam to heat and melt materials, which are then fused together as they cool. This process relies on the principle of converting laser energy into heat at the point of contact between the materials to be joined. There are two main types of laser welding processes:
Conduction Mode Welding:
In this mode, the laser beam’s power is relatively low, and the heat generated is conducted through the materials being welded. It is typically used for materials with high thermal conductivity, such as copper or aluminum.
Keyhole Mode Welding:
In this mode, the laser beam’s power is significantly higher, creating a deep, narrow hole (keyhole) in the materials. The intense heat generates vapor and plasma within the keyhole, which helps to create a strong weld. This mode is suitable for welding thicker materials and those with lower thermal conductivity, like stainless steel or titanium.
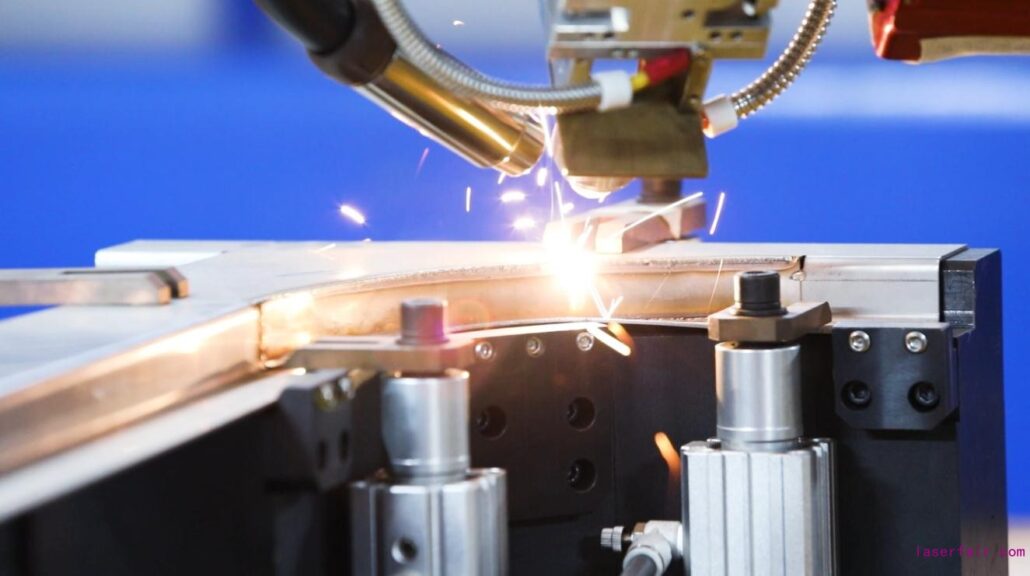
Laser Welding Techniques
Laser welding offers several techniques to meet specific requirements:
Spot Welding:
This technique involves creating small, localized welds with pinpoint accuracy. It’s commonly used in the automotive industry for joining thin sheets of metal.
Laser Seam Welding:
Seam welding utilizes a laser beam to create a continuous weld along the entire length of a joint. It is ideal for joining materials with long seams, such as pipes or tubes.
Laser Micro Welding:
This technique is used for extremely fine and delicate work, such as in the medical and electronics industries. It requires precise control and is capable of creating minuscule welds.
Laser Hybrid Welding:
Combining laser welding with other welding methods, such as gas metal arc welding (GMAW) or gas tungsten arc welding (GTAW), enhances the process’s efficiency and flexibility.
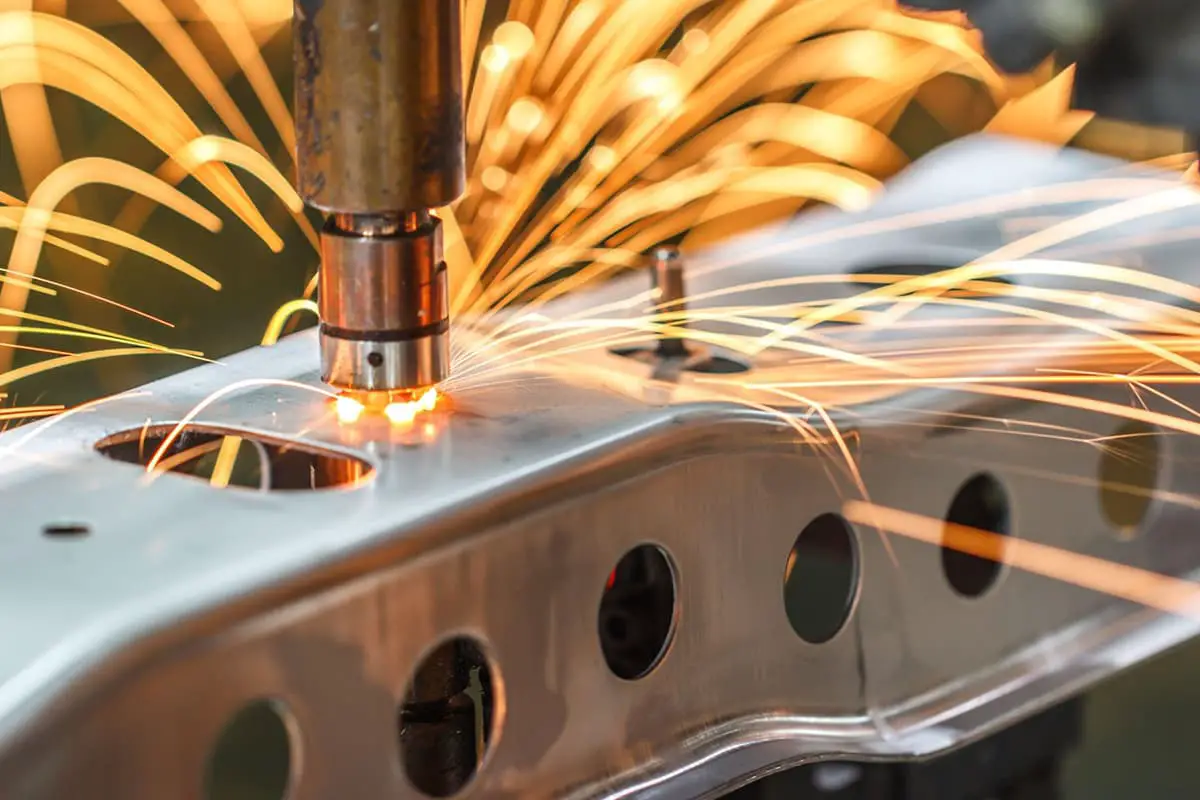
Applications of Laser Welding
Laser welding finds application in various industries due to its versatility, precision, and ability to work with a wide range of materials. Some notable applications include:
Automotive Industry:
Laser welding is extensively used in automotive manufacturing for joining body panels, exhaust systems, and other components. It improves structural integrity and reduces weight, contributing to better fuel efficiency.
Aerospace Industry:
Laser welding is crucial for aerospace applications, as it enables the creation of lightweight, high-strength joints in materials like titanium and aluminum, commonly used in aircraft and spacecraft construction.
Medical Devices:
The medical industry relies on laser welding for creating precise, hermetically sealed connections in medical instruments and implants, ensuring biocompatibility and sterilizability.
Electronics:
Laser welding is used in the electronics sector for soldering components on printed circuit boards (PCBs), creating durable and reliable connections.
Energy Sector:
It plays a pivotal role in the fabrication of solar panels, batteries, and heat exchangers for renewable energy systems.
Jewellery Manufacturing:
Laser welding offers jewelers a precise method for repairing and crafting intricate jewelry pieces.
