Custom metal part manufacturing involves creating tailor-made metal components that meet specific requirements in terms of design, functionality, and performance. Unlike mass production, custom manufacturing emphasizes precision, flexibility, and adaptability, enabling the production of unique components suited for niche applications or prototypes.
From intricate aerospace components to robust industrial machinery parts, custom metal part manufacturing plays a pivotal role in numerous industries. This article delves into the essential processes, materials, techniques, and advancements in this field, highlighting its significance and versatility.
Importance of Custom Metal Part Manufacturing
Tailored Solutions
Custom metal parts are designed to meet precise specifications, ensuring optimal performance in their intended applications.
Enhanced Functionality
Components can be designed to accommodate unique operational demands, such as high load-bearing capacity, extreme temperature resistance, or lightweight construction.

Prototyping and Innovation
Custom manufacturing supports rapid prototyping, enabling businesses to test and refine designs before committing to large-scale production.
Cost Efficiency
While the initial cost may be higher, the elimination of unnecessary features and precise material usage often result in long-term cost savings.
Compatibility
Custom parts can seamlessly integrate into existing systems, reducing the need for modifications or additional components.
Key Processes in Custom Metal Part Manufacturing
Custom metal manufacturing encompasses a range of processes designed to shape, cut, join, and finish metal components. Each process is chosen based on the material properties, design complexity, and intended application.
Cutting Processes
Cutting involves shaping metal into desired dimensions and geometries.
Laser Cutting
Process: Uses a focused laser beam to cut through metal with high precision.
Advantages:
Suitable for intricate designs.
Minimal material waste.
High-speed operation.
Applications: Decorative panels, precision machinery components.
Waterjet Cutting
Process: High-pressure water mixed with abrasive materials is used to cut metal.
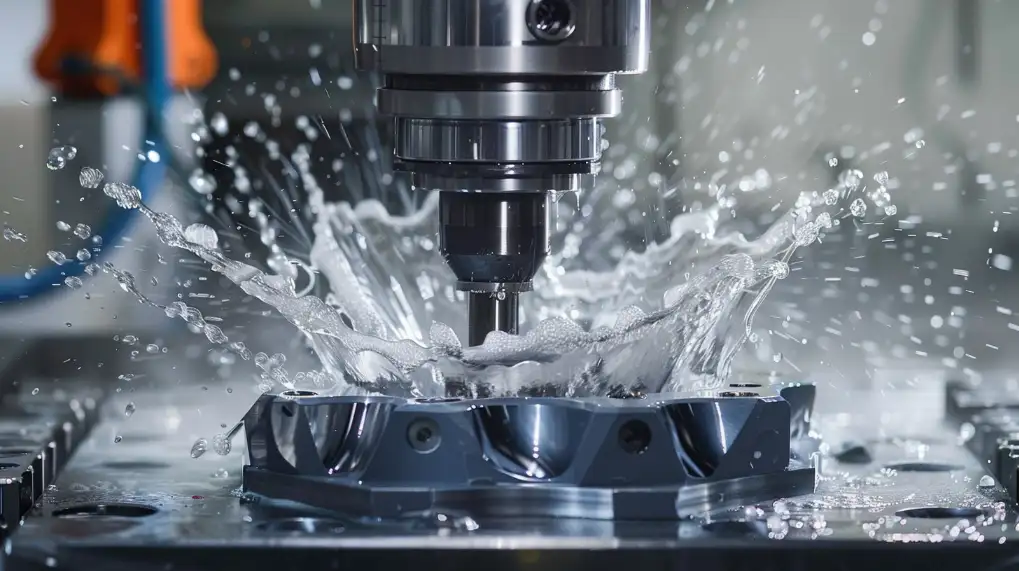
Advantages:
Cold cutting process eliminates heat-affected zones (HAZ).
Suitable for thick and delicate materials alike.
Applications: Aerospace components, automotive parts.
Plasma Cutting
Process: An electric arc generates high-temperature plasma to cut through electrically conductive metals.
Advantages:
Fast and efficient.
Works well on thicker materials.
Applications: Structural steel parts, industrial equipment.
CNC Machining
Process: Computer Numerical Control (CNC) machines use rotating tools to cut, drill, and shape metal.
Advantages:
Exceptional precision.
Repeatable results for complex geometries.
Applications: Prototyping, medical implants, and aerospace parts.
Forming Processes
Forming processes shape metal by deforming it without removing material.
Bending
Description: Applies force to sheet metal to create angular or curved shapes.
Applications: Brackets, frames, enclosures.

Deep Drawing
Description: Pulls a metal sheet into a die to form complex hollow shapes.
Applications: Automotive body panels, cookware, and canisters.
Roll Forming
Description: Continuous bending of metal strips to achieve long, uniform shapes.
Applications: Roofing panels, structural profiles.
Stamping
Description: Uses a stamping press and dies to cut, punch, or emboss metal.
Applications: Electrical enclosures, decorative elements.
Joining Techniques
Joining processes combine metal parts into assemblies.
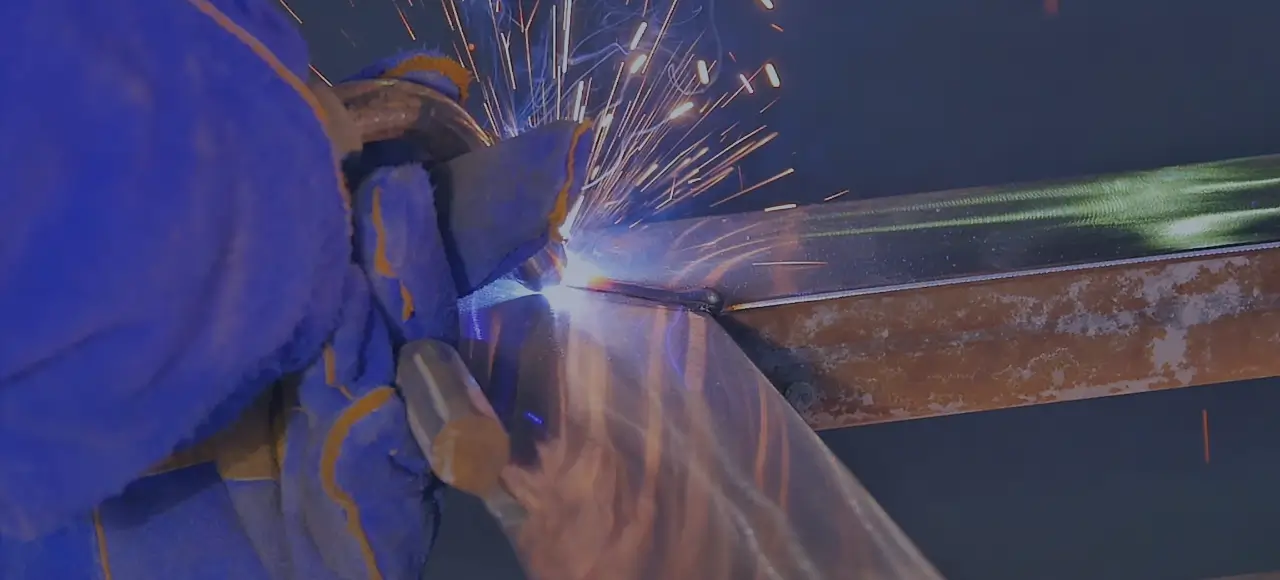
Welding
Description: Fusion of metal parts through heat, pressure, or both.
Types:
TIG Welding: Precision welding for thin metals.
MIG Welding: Suitable for thicker metals and faster applications.
Spot Welding: Common for sheet metal assemblies.
Applications: Automotive frames, pipelines, heavy machinery.
Riveting
Description: Uses rivets to fasten parts together without fusion.
Applications: Aerospace structures, bridges.
Adhesive Bonding
Description: High-strength adhesives join metal parts without altering their physical properties.
Applications: Lightweight assemblies, electronics.
Surface Finishing
Surface finishing enhances appearance, functionality, and durability.
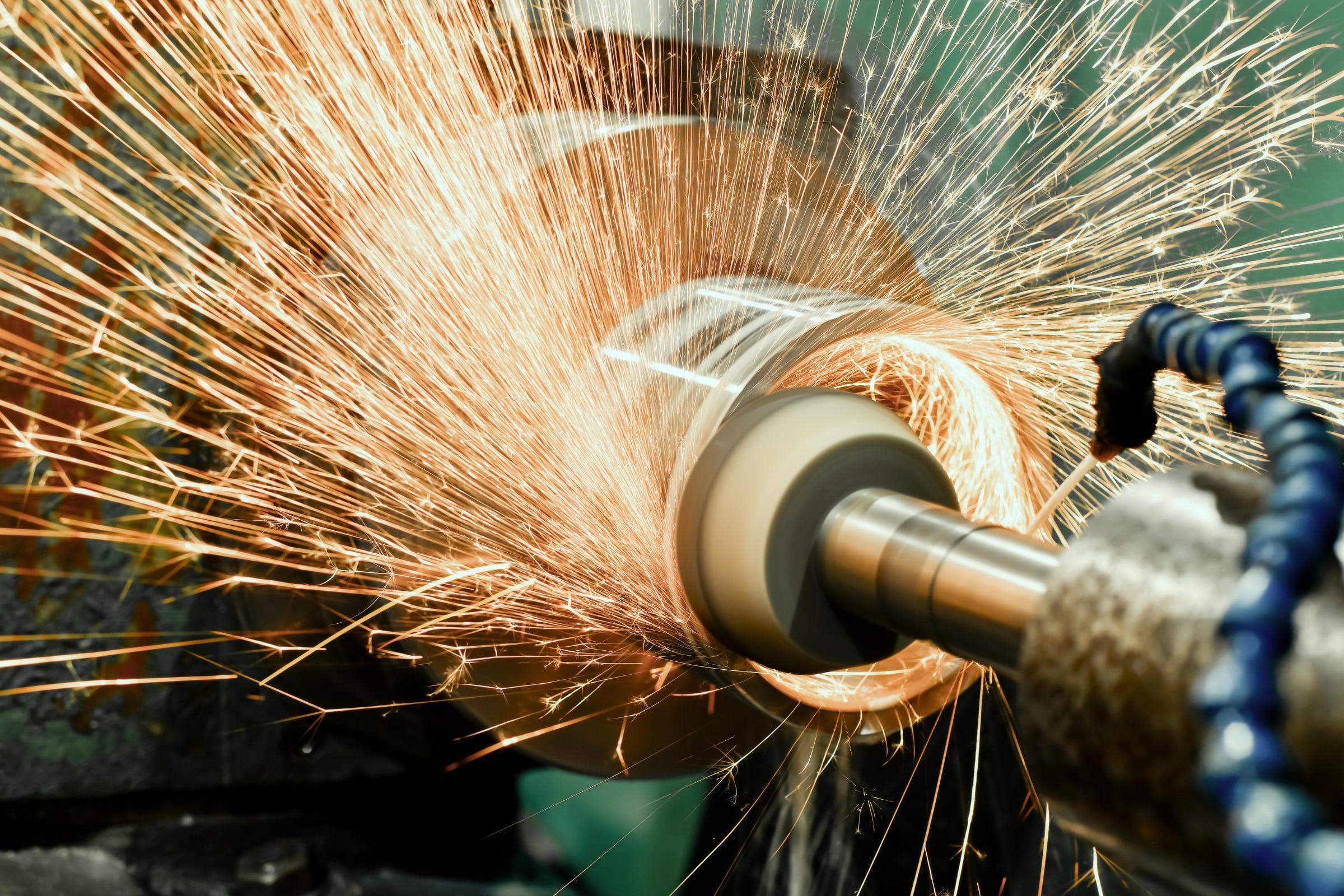
Powder Coating
Description: Electrostatically charged powder is applied to metal surfaces and cured.
Advantages: Durable and aesthetically appealing finishes.
Applications: Automotive parts, outdoor furniture.
Electroplating
Description: A metal coating is applied via an electrochemical process.
Applications: Decorative hardware, corrosion-resistant parts.
Anodizing
Description: A controlled oxidation process enhances aluminum’s surface.
Applications: Aerospace components, consumer electronics.
Materials for Custom Metal Parts
The choice of material is crucial for achieving the desired mechanical properties, functionality, and cost-effectiveness.
Ferrous Metals
Steel: Versatile and widely used for its strength and durability.
Stainless Steel: Resistant to corrosion, ideal for medical and food-grade applications.
Non-Ferrous Metals
Aluminum: Lightweight, corrosion-resistant, and highly formable.
Copper: Excellent thermal and electrical conductivity.
Titanium: High strength-to-weight ratio and biocompatibility.
Alloys
Nickel Alloys: Heat-resistant and ideal for high-performance applications.
Magnesium Alloys: Lightweight and used in aerospace and automotive industries.
Applications of Custom Metal Parts
Custom metal parts find applications in various industries, such as:
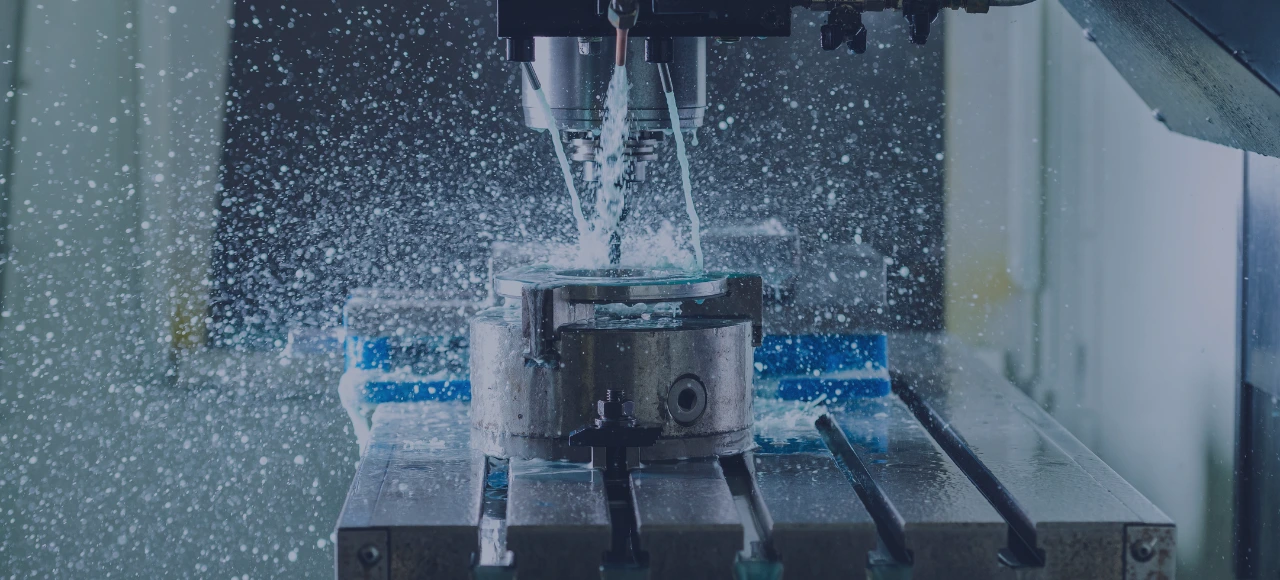
Automotive
Engine components, exhaust systems, and chassis parts.
Aerospace
Structural elements, turbine blades, and landing gear components.
Healthcare
Surgical instruments, implants, and diagnostic equipment.
Electronics
Heat sinks, casings, and connectors.
Construction
Beams, brackets, and roofing components.
Advancements in Custom Metal Manufacturing
The field has witnessed significant technological advancements:
Additive Manufacturing
3D metal printing enables the creation of complex, lightweight designs.
