Robot welding is the use of mechanized programmable tools, which completely automate a welding process by both performing the weld and handling the part. It’s commonly used for resistance spot welding and arc welding in high production applications, such as the automotive industry.
The major components of arc welding robots are the manipulator or the mechanical unit and the controller, which acts as the robot’s “brain”. The manipulator is what makes the robot move. The robot may weld a pre-programmed position, be guided by machine vision, or by a combination of the two methods.
Advantages of robot welding include increased productivity, decreased risk of injury, lower production costs, reduced cost of labor, consistent quality, and reduced waste. However, there are also disadvantages such as lost jobs and wages, high cost of machinery and installation, cost of specialized training, limited functionality, and delayed quality control.
Robotic welding is considered to be the most productive when it is implemented for high-volume and repetitive tasks. These robots can reach locations that are inaccessible by human hands and perform complicated tasks much more precisely. Therefore, the time taken in the manufacturing process is minimized and greater flexibility is achieved.
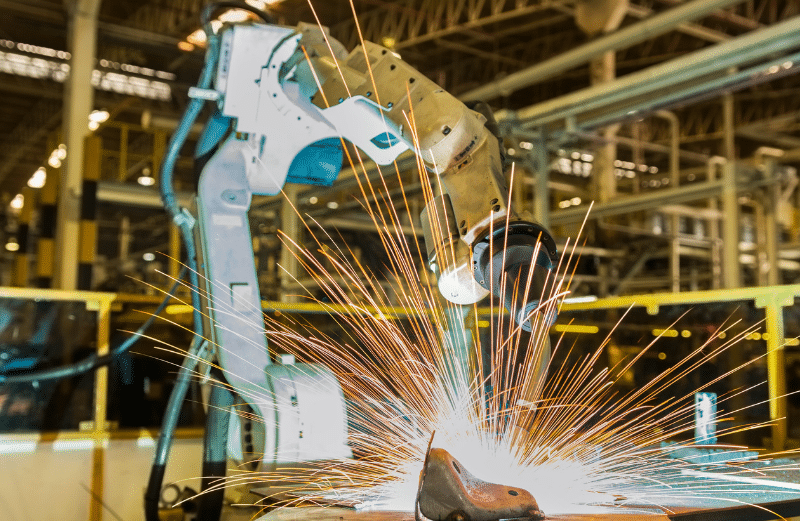
How does robotic welding work?
Robotic welding works by using mechanized programmable tools, which completely automate a welding process by both performing the weld and handling the part. Here’s a basic breakdown of how it works:
➤ Programming: The robot is programmed to perform and manage welding tasks based on the intended project. This programming can be adjusted as per the requirements of different projects.
➤ Positioning: The robot identifies the weld points and moves the robotic welding arm and torch to the correct areas. The robot may weld a pre-programmed position, be guided by machine vision, or by a combination of the two methods.
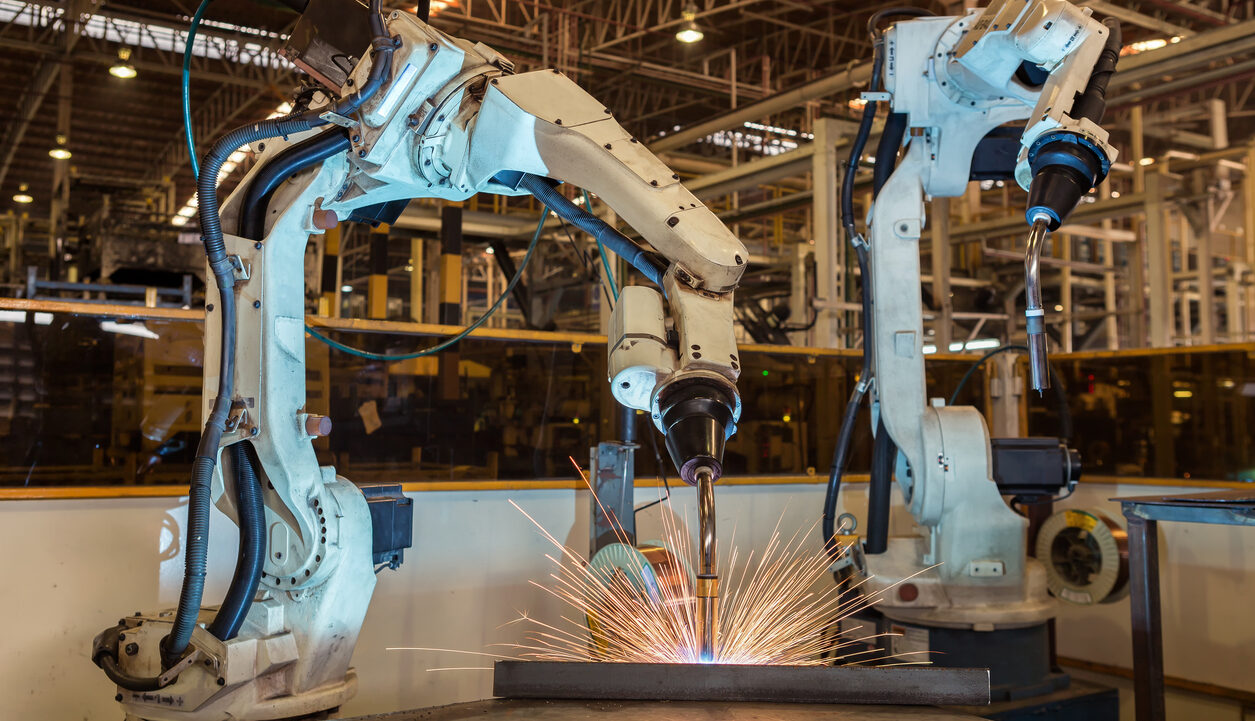
➤ Welding: Welding robots, in particular, incorporate an arm that is capable of moving in three dimensions and welding metals together. There is a wire feeder that sends a filler wire to the robot, and a high-heat torch towards the end of the arm that melts metals during the welding process.
➤ Post-Welding: After completing the weld, the machine stops and the welded parts can be removed from the fixture. The robotic welding arm moves the torch to a cleaning station, where metal splatter is removed to maintain the integrity of future welds.
➤ Supervision: Despite the automation, human intervention is not completely eliminated as welders still control and supervise the welding robots.
What are the advantages of robotic welding?
Robotic welding offers several advantages, including:
➤ Increased Productivity: Robotic welding systems can operate continuously, leading to significantly higher productivity compared to manual welding.
➤ Decreased Risk of Injury: Since the robot performs the welding task, the risk of injury associated with human interaction is greatly reduced.
➤ Lower Production Costs: The efficiency and speed of robotic welding can lead to lower production costs over time.
➤ Reduced Labor Costs: Robotic welding requires less human labor, which can lead to savings in labor costs.
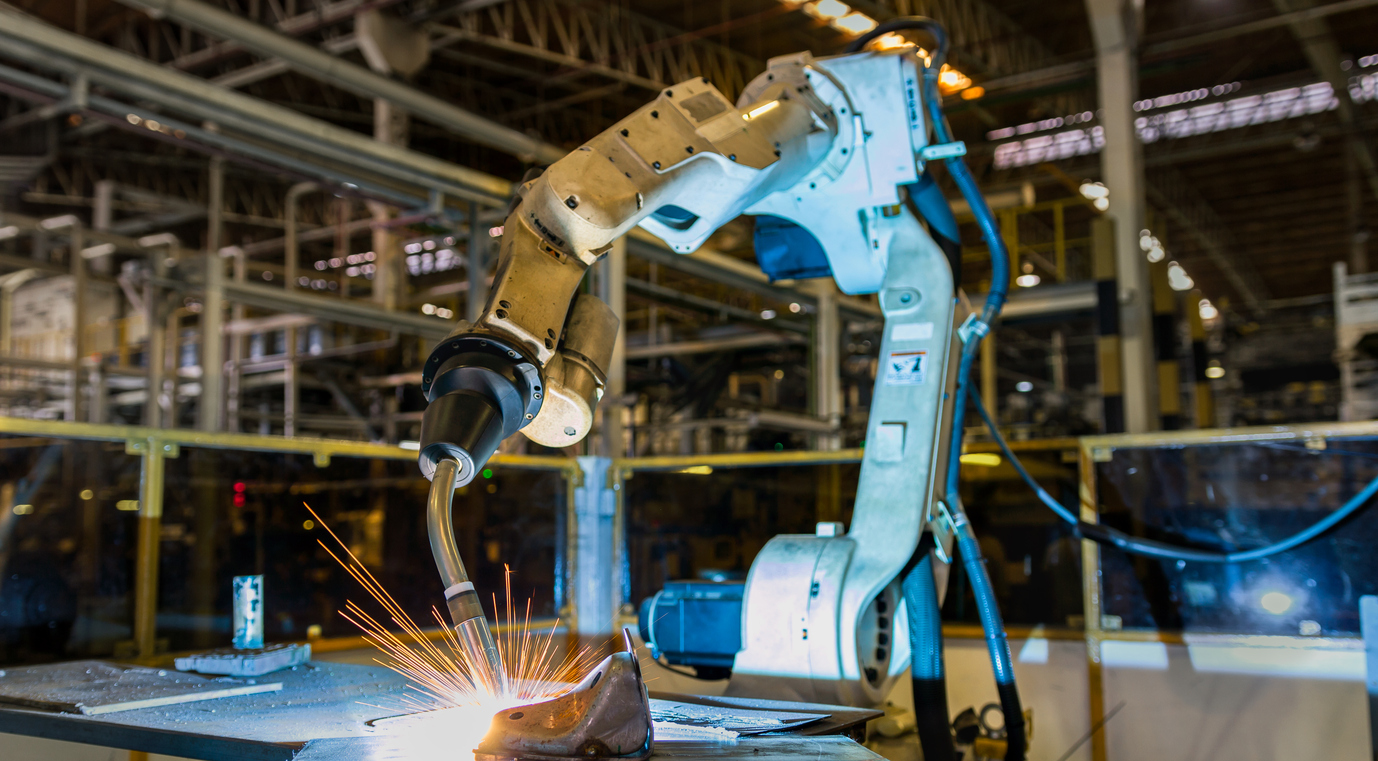
➤ Consistent Quality: Robots can produce welds of consistent quality, reducing the rate of error and rework.
➤ Reduced Waste: With their precision and consistency, robots can reduce waste in the welding process.
➤ Greater Flexibility: These robots can reach locations that are inaccessible by human hands and perform complicated tasks much more precisely. Therefore, the time taken in the manufacturing process is minimized.
However, it’s important to note that there are also disadvantages such as lost jobs and wages, high cost of machinery and installation, cost of specialized training, limited functionality, and delayed quality control.
How does robotic welding compare to manual welding?
Robotic welding and manual welding each have their own advantages and disadvantages, and the choice between the two often depends on the specific requirements of the project.
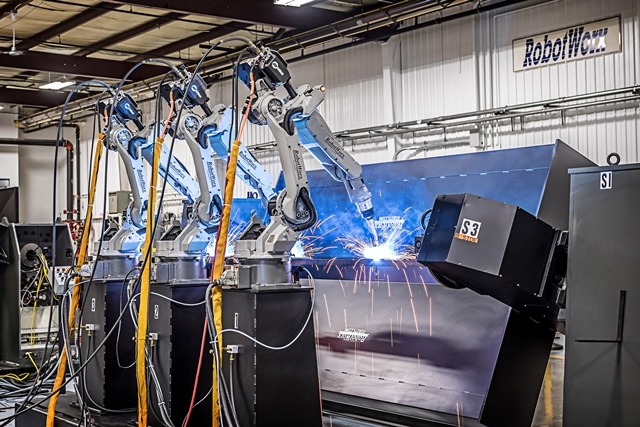
Robotic Welding:
✓ Pros:
➤ Increased Output: Robots work more quickly and accurately than humans, and they can also complete multiple welds simultaneously, resulting in increased productivity and output.
➤ Improved Quality: Robotic welding is an extremely reliable process with high-quality results.
➤ Safety: Welding environments are often harsh and filled with toxic fumes. Robotic welding helps eliminate the dangers to employees.
➤ Less Waste: The efficiency and accuracy of robotic welding means that less material is needed and wasted during the welding process.
➤ Reduced Costs: Robotic welding of either type means fewer human workers to pay.
✓ Cons:
➤ Lack of Flexibility: Robotic welding works well for simple, repeated tasks, but it is not nearly as adaptable as manual welding.
➤ Dependence: If your company is dependent on robotic welding, it can be highly problematic if there are technical issues with the robots.
➤ High Cost: You won’t have to pay as many human workers, but you will have to pay high upfront costs for initial setup and maintenance.
Manual Welding:
